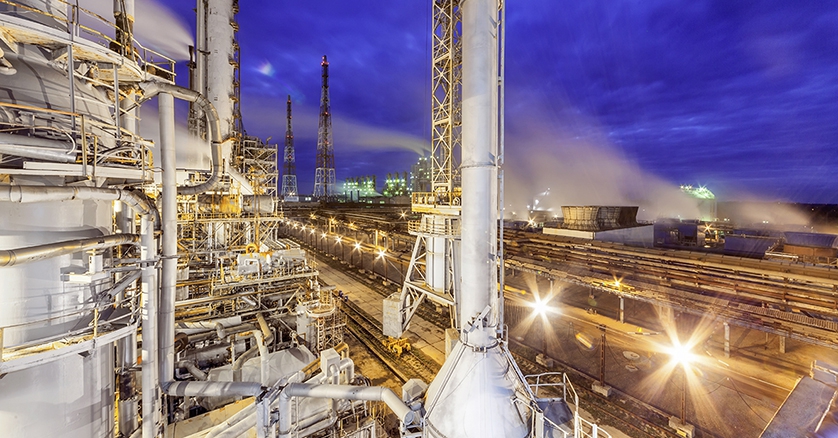
Vacuum tower revamps and internal upgrades can improve the yield and product quality of vacuum distillation units (VDU), a must in today’s competitive markets. These modifications, though, require a considerable influx of capital. Improvements in cross sectional tower temperature measurements allow evaluating the effectiveness of the tower’s original internals, verifying yield and product quality, and helping to decide if an upgrade is financially justified.
New process equipment, however, does not reduce the need for careful operational control and accurate field measurement of parameters to ensure optimal conditions. Proper operation of VDUs will increase their lifetime, minimize shutdowns and downtime, and protect the big investment associated with this type of implementations.
To improve yield and quality product, modern designs for tower internals emphasize even distribution of the vapor feed and elimination of liquid entrainment, the undesirable liquid that forms from residue droplets and resists separation from the vapor feed as it rises in the vacuum tower. Well planned VDU revamps now include low-cost, high value field instrumentation such as advanced, flexible, temperature measurement systems above the wash oil distributor to detect and control wash bed coke formation and identify rogue residue entrainment approaching HVGO draw-off. These relatively inexpensive additions ensure that the vacuum tower works at its best and they prevent unnecessary shutdowns.
The System
The feedstock to the vacuum tower/vacuum distillation column is a superheated, two-phase stream coming from the bottom ends of the atmospheric crude distillation column. Upon entry into the vacuum tower, the feed separates into a rising vapor stream and a falling liquid stream. The rising vapor stream is separated into two or three vacuum gas oil cuts that feed downstream catalytic conversion units. The falling liquid stream, or residue, contains measureable amounts of nickel and vanadium metals along with hydrogen deficient molecules (Conradson carbon residue, or CCR). During the separation of the two-phase vacuum tower feed, a portion of the liquid residue does not fully separate from the vapor and will rise along with the vapor stream. This entrained, contaminated stream, if allowed to reach the first vacuum gas oil draw-off (heavy vacuum gas oil, or HVGO), will have poisonous effects on the catalysts of downstream conversion units.
Vacuum towers have a vapor distribution system consisting basically of a distributor, typically a horn, and a wash bed and wash oil distributor that enhance feed vapor distribution and eliminate liquid residue entrainment from the passing vapor stream. This distribution system is the primary defense against entrained residue liquids reaching the HVGO draw off.
The wash bed, comprised of a packing set below a wash oil distributor, is below the HVGO draw-off. The wash bed packing provides significant surface area for the vapor to pass along and deposit the entrained residue. As long as the packing maintains a proper level of wetness, it will de-entrain effectively and there will be no coke formation caused by dry out from the passing vapor. The packing is wetted by a cool stream of wash oil reflux moving downward against the vapor flow and distributed over the wash bed packing. The cool reflux facilitates condensing and separation of the entrainment while allowing the super-heated vapor to continue its rise through the column and inhibiting coke formation.
The Problem
The wash bed packing must keep a proper level of wetness to de-entrain correctly and avoid coke formation. A cool wash oil reflux is introduced above the wash bed through a wash oil distributor to facilitate condensation of the rising vapor stream and to maintain the minimum level of liquid on the packing. If the rate of wash oil distributed over the wash bed is too high, the wash bed risks condensing both the entrainment and significant portions of the vapor stream intended to condense later in more elevated sections of the vacuum tower. Such “over condensation” reduces the VGO product quantity leaving the wash bed. On the other hand, if the rate of wash oil reflux is too low, the super-heated vapor overpowers the cooling effect of the cool wash oil, creating dry outs at locations where the wash oil wetting is below proper levels. Once a section of the packing is dry, condensed entrainment droplets can quickly form coke on the wash bed packing.
Coke formation attracts and redirects vapor flow to the coked region, creating localized, above average flow rates of the super-heated vapor and liquid entrainment to the already dry and coked section. Such process not only exacerbates coke formation in certain areas but also disturbs vapor distribution and can reduce the efficiency of the downstream fractions in the top parts of the vacuum tower. As the distribution worsens, the vapor flow rate increases to a point when the wash bed can no longer de-entrain the liquid contaminants which then bypass the wash bed and enter into the HVGO draw-off pool. This maldistribution continues past the wash bed/wash oil distributor. An uneven distribution of the vapor flow causes an uneven temperature differential across the cross section above the wash oil distributor.
Coke formation, if not properly controlled, escalates and will require the shutdown of the vacuum tower, affecting downstream conversion units and causing downtime and associated financial losses. This series of events can occur over an extended period of time or quite rapidly but they can be prevented.
The Solution
Early knowledge of maldistribution of vapor flow above the wash bed allows changing wash oil feed rates and/or vapor feed rates into the vacuum tower and controlling coke formation. If the vacuum tower operator can measure the trending temperature differential (delta-T, or ∆T) at different points of given cross sectional areas above the wash oil distributor, he can detect maldistribution of the vapor through the wash bed caused by coke formation. Using this early warning signs, the operator can then make adjustments and modify wash oil and other feed rates into the vacuum tower, effectively preventing coke formation and poor de-trainment. When designed and installed properly, an advanced temperature measurement system is a reliable tool for identifying differential temperatures with certainty, allowing adjusting the wash oil feed rate as necessary, based on analysis of the trending data over an established period of time.
Measurement of cross sectional temperature differentials in high temperature refining, petrochemical, and chemical applications is best accomplished with a flexible multi-sensor temperature measurement system. This technology allows the insertion of more than 45 sensors specifically located at an elevation/cross sectional area through a single DIN-75 (3 inch) nozzle. This type of measuring system will provide the data needed to control coke formation.
With proper installation of a flexible multiple sensor system above the wash bed, operators can take advantage of the relationships between coke formation, maldistribution of vapor flow, and differential temperature trends to control certain aspects within the vacuum tower. They can then modify feed rates, preventing potential reductions in yield and product quality, ensuring the VGO works under optimal conditions and protecting your investment.