
Venturi nozzles help regulate feedstock flow rates in order to minimize uneven coking inside the radiant tube walls of furnaces. Along with tubeskin thermocouple assemblies, Venturi nozzles enable ethylene crackers to operate more efficiently.
Refineries and petrochemical plants are familiar with WIKA’s many temperature measurement solutions – our multipoint thermocouple assemblies and other electronic temperature sensors are the go-to options for hydrocrackers, hydrotreaters, steam methane reformers, and distillation units. But our instruments for process industries do not stop there. WIKA also manufactures critical Venturi nozzles and other primary flow elements for ethylene crackers.
Steam cracking process in ethylene production
The most common way to obtain ethylene (C2H4) is to use steam to break the long carbon chains of ethane (C2H6) and other hydrocarbons. This is pyrolysis, or steam cracking – a very demanding process with some of the harshest working conditions in the industry.
A typical cracking furnace has one or two rectangular fireboxes with vertical radiant coils in the center between two radiant refractory walls. These radiant coils superheat the hydrocarbon feedstock and the steam stream, with the reaction products in the tubes reaching temperatures of up to 1,560°F (850°C). In addition to extremely high temperatures, steam crackers must also deal with high pressures and corrosive media.
What is coke formation in thermal cracking?
A major challenge of ethylene production is coke formation during steam cracking. Coking and fouling occur when the high-boiling-point molecules formed during cracking collect inside radiant furnace tubes and then polymerize. This coke layer increases the temperature of furnace tubes, and the results are additional pressure drops, reduced yield, increased energy consumption, and shortened tube life.
What determines how much coke is formed on tube walls?
The amount of coke formed on a furnace’s tube walls is a function of several factors:
- Intensity of the cracking
- Unfired residence time of the feed
- Final boiling point of the heaviest molecules in the feed
- Temperature to which the cracked gas is cooled in the transfer line exchanger
- Temperature of the transfer line exchanger cooling
- Unbalanced distribution of feedstock flow
To address the last point, plant operators can install a radiant (or crossover) critical Venturi nozzle at the inlet of each radiant coil to make sure the flow through the coils is even.
How Venturi nozzles improve ethane furnace operations
Based on the principle of Venturi nozzles working with critical flow, flow is independent of the pressure downstream of the nozzle. As long as the pressure ratio (Pout/Pin) in the Venturi nozzle is below 0.85, the critical flow is maintained and coil coking is relatively uniform. The critical Venturi nozzles ensure equal flow distribution and equal residence time in all parallel coils of the furnace, even when there is uneven coking and pressure drops in one or more coils.
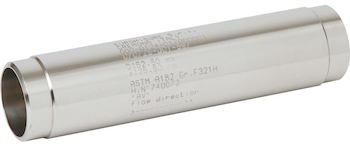
Critical Venturi nozzle
WIKA’s critical Venturi nozzles are bar forged from highly temperature-resistant austenitic stainless steels like SS321H, SS304H, or SS347H in size ranges from 1.25″ to 5″. We optimize critical Venturi nozzles for each furnace’s tubes, and then retrofit them to steam cracking furnaces. When these primary flow elements are used in conjunction with our temperature sensors, ethylene plants will see less coking and greater efficiency.
WIKA has installed critical Venturi nozzles and thermocouple assemblies in chemical plants all over the world. We also have a large portfolio of instruments for measuring pressure and level. Contact WIKA USA if you would like a comprehensive monitoring system designed for your specific facility.
Product mentioned in this article: