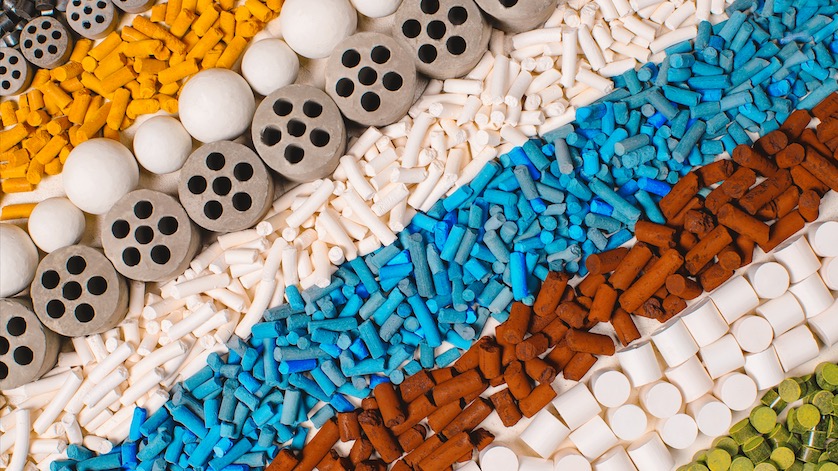
A major producer of supported catalysts in the U.S. was dissatisfied with the short lifespan of the temperature sensors in their rotary calciners. WIKA USA came up with a creative solution that protects thermocouples from mechanical damage while still providing accurate readings and a fast reaction time.
Catalysts are an essential part of downstream oil and gas activities, including syngas production and refinery processes like hydrocracking, and fluid catalytic cracking (FCC). The manufacturing of food, pharmaceuticals, chemicals, and petrochemicals also rely on catalysts.
What Catalysts Do
Available in myriad forms and formulations, catalysts are substances that accelerate and optimize chemical reactions by lowering their activation energy. By using a catalyst, temperatures and pressures do not need to be as high, thus saving manufacturers significant time and energy. Other features of catalysts are that they enhance reactions without being wholly consumed, and can be put back into service after being treated with heat, hydrogen, acid or alkaline solutions, or another regenerative process, although they will eventually need to be replaced.
Most of the hundreds of catalysts used in manufacturing are supported catalysts, in which the active component, such as a metal or metal oxide, is bonded to a carrier substrate. Support materials include alumina, activated carbon, ceramic, various polymers, silica, zeolite, and zirconia. The ideal supports are:
- Porous, so that the catalyst has plenty of surface area to be deposited upon, as more catalytic material means more encounters with the reactant molecules
- Pure and inert, so as to not create secondary chemical reactions
- Mechanically strong, as a hard material holds up better during industrial processes and catalyst regeneration
Supported catalysts are usually produced by calcination in rotating kilns, also called rotary calcinators or rotary calciners.
How Catalysts Are Made in Rotary Calciners
Calcination, specifically in a rotary calciner, is just one of several steps in large-batch catalyst production. The specific manufacturing method depends on the type of catalyst being made. In general, these are the steps.
- Raw material preparation: Particles of ceramics, metals, and/or polymers are mixed with a solution to create a suspension of catalyst and support materials.
- Hydrothermal treatment: The suspension is poured into a reactor, where it is heated and agitated until the support material is impregnated with catalyst atoms. The reactor then dries the resulting crystals until it reaches a powdery state.
- Shaping: The powder is mixed with a binding agent, and the resulting paste is usually fed into an extruder. This catalyst precursor can also be pelleted or tableted. The shaped size and form have an impact on its performance and structural strength.
- Calcination: The shaped catalysts are fed into a calcinator, a kiln that applies high heat to further dry and harden the material and to burn off impurities. Calcination can also change the catalyst’s phase, increase its surface area, and/or activate it. A rotary calciner provides continuous agitation as the catalyst moves down the revolving vessel and is exposed to increasingly higher temperatures, resulting in a higher-quality, more uniform product.
- Reduction: Once calcined, the catalyst may pass through a reducing atmosphere to remove oxygen from metal oxide. This ensures that the catalyst is in the correct state.
- Activation: If calcination did not sufficiently activate the catalyst, the next step is to treat it with a reactant.
- Packaging; Now pure and ready for use, the final product is placed in drums, sealed to prevent contamination, and then shipped to the client.
Problem: Measuring High Temperatures in a Rotary Calciner’s Challenging Conditions
Industrial rotary kilns allow for large quantities of catalysts to be calcined effectively and efficiently. Key to this step are temperature sensors, as proper thermal treatment of catalysts requires precise temperature monitoring and control. Data are fed to a computerized control system, which adjusts the air flow and fuel input as necessary to maintain optimal thermoprocessing conditions.
Rotary calciners present a combination of measuring challenges not found in many other applications:
- Temperatures can get as high as 1,830°F (~1,000°C), which shortens the service life of sensors that are not designed for such extreme conditions.
- Hardened catalyst pellets, as they are tossed by the rotating drum, repeatedly knock against the temperature probe and damage it over time.
- Most temperature sensors are inserted individually through the vessel wall via flanges. A rotating vessel creates challenges in terms of wiring placement.
The U.S. manufacturing facility of a European catalysis and process technology company was having a hard time finding a temperature solution that not only would provide an accurate temperature profile of their indirect-fired rotary calciners, but also withstand the logistical and media challenges of the application. In the kiln’s original design, the thermocouples did not meet the customer’s lifespan expectations, even though a thermowell shielded each sensor.
Solution: An Innovative Pipewell Assembly to Replace Individual Flanges
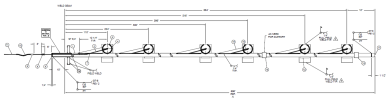
WIKA’s custom-engineered temperature assembly for a rotary calciner used in catalyst production (click to enlarge)
The catalyst manufacturer reached out to WIKA USA, and our temperature experts performed a site visit to review the application. The large rotary calciner, roughly 60 feet (18 meters) long, had six flanged temperature sensors inserted along the vessel’s length. They asked if we could come up with a better way to measure the unit’s internal temperatures while protecting the sensors from the hard catalyst pellets.
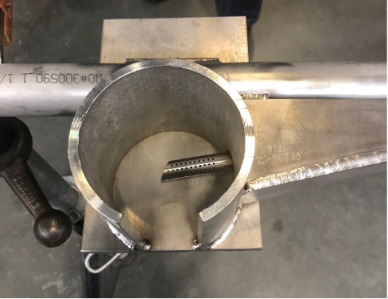
Cross-section of the semi-open protective chamber, showing a perforated insertion tube
Inserted into each perforated tube was a thermocouple, which has a faster reaction time and higher temperature range than RTDs. Opting for grounded thermocouples resulted in an even faster reaction time to temperature changes, and using the popular Type K thermocouple meant corrosion resistance, a stable output, and a high temperature range – up to 2,300°F (1,260°C) – at an affordable price point. WIKA’s T32 digital temperature transmitter relayed temperature data back to the facility’s central control system.
Result: Long-Lasting Thermocouples for Thermoprocessing Equipment
After this assembly was installed in this customer’s rotary calciners, the specially engineered multipoint sensors have monitored the units’ internal temperatures without fail. In fact, the catalyst plant was able to increase the lifespan of its temperature sensors from a few months to three years and counting, resulting in a significant reduction in operating expenses in addition to greater safety and efficiency due to precise temperature monitoring and control. Since installing our specially engineered temperature assemblies, the catalyst manufacturer has made this design a part of their site specifications.
WIKA USA, Smart in Sensing for Catalyst Manufacturing
The product specialists at WIKA have decades of experience in designing innovative solutions for even the trickiest measurement challenges. We work closely with customers to understand their issues, then engineer and install assemblies that maximize a plant’s operations, increase safety, and reduce expenses. What’s more, we follow up regularly to finetune the assembly, and provide replacement and installation services when the sensors reach the end of their natural lifespan.
Contact us for more information about sensor solutions for rotary calciners and other high-temperature applications.
Products and services mentioned in this blog• Engineered temperature solution
• T32 digital temperature transmitter with HART® communication protocol
• Field services for temperature applications